Vier-Wege-Multi-Shuttle-System
Einführung
Intelligente Logistik ist eine integrierte Szenarioanwendung automatisierter und intelligenter Technologie, die alle Verbindungen aktiviert, eine erhebliche Steigerung der Lagerraumkapazität effektiv realisiert und die Lagerung, Lieferung, Sortierung, Informationsverarbeitung und andere Vorgänge von Teilen schnell und genau umsetzt.Durch die Analyse der Überwachungsbetriebsdaten können wir die geschäftlichen Schwachstellen genau erfassen, die Geschäftsfähigkeiten weiter optimieren, Kosten senken und die Effizienz steigern.Der Einsatz von Technologie und Big-Data-Analyse auf der Grundlage intelligenter Logistik wird zur Hauptrichtung der Entwicklung der Teilelogistik als wichtiger Indikator zur Messung des Niveaus des Betriebs und Managements der Unternehmenslogistik.
Systemvorteile
1. Helfen Sie Unternehmen, deutlich Kosten zu sparen
Der Einsatz eines Vier-Wege-Multi-Shuttle-Systems nutzt die Höhe des Lagers voll aus, um eine intensive Lagerung von Materialien zu realisieren und die Effizienz zu verbessern.Das automatisierte Intensivlager und das vordere Fördersystem senken die Arbeitskosten, verringern die Arbeitsintensität und verbessern die Effizienz.
2. Sicherer Betrieb
Ergonomische Kommissionierplätze können die Leistung des Bedieners verbessern und die Fehlerquote senken.
3. Erhöhte Verarbeitungskapazität
Die Lagerumschlagskapazität ist zwei- bis dreimal so hoch wie die eines herkömmlichen automatisierten Lagers.
4. Verbesserungen bei der Informationskonstruktion
Realisieren Sie das gesamte Prozessmanagement von Materialien im und aus dem Lager durch Methoden des Informationsmanagements.Gleichzeitig verfügt es über eine zugehörige Abfrage- und Berichtsverwaltung, um Datenunterstützung für die Lagerverwaltung bereitzustellen.
5. Flexibel, modular und erweiterbar
Je nach Geschäftsbedarf können flexibel weitere Shuttles hinzugefügt werden, um die Effizienz zu verbessern.
Anwendbare Branche: Kühlkettenlagerung (-25 Grad), Gefrierlager, E-Commerce, DC-Center, Lebensmittel und Getränke, Chemie, Pharmaindustrie, Automobilindustrie, Lithiumbatterien usw.
Kundenfall
NANJING INFORM STORAGE EQUIPMENT (GROUP) CO.,LTD stellt einem bekannten Automobilunternehmen eine einfach erweiterbare kastenförmige Vier-Wege-Multi-Shuttle-Systemlösung zur Verfügung, um das Unternehmen bei der Optimierung des automatisierten Lagersystems zu unterstützen, um eine hohe Raumausnutzung zu erreichen , schnelle Frachtlagerung und präzise Anforderungen an die Eingangs- und Ausgangskontrolle, um die Pünktlichkeit der Auftragsantwort sicherzustellen, die Effizienz des Unternehmens zu verbessern und effektiv Personal- und Betriebskosten einzusparen.
Das bekannte Automobilunternehmen, mit dem INFORM dieses Mal zusammengearbeitet hat, ist ein aktiver Praktiker der intelligenten Logistik in der Autoteileindustrie.Das Unternehmen ist hauptsächlich für den Betrieb des After-Sales-Ersatzteil-Zentrallagers verantwortlich.Bisher wurden für die Lagerung mehrstöckige Zwischengeschosse und Palettenregale genutzt.Da es immer mehr Kategorien von Ersatzteilen gibt, gibt es immer noch viele Probleme in der Lagerhaltung, Kommissionierung und im Warenausgangsprozess, die durch intelligente logistische Lagerlösungen gelöst werden müssen.Nach vielen Überlegungen kann die von INFORM bereitgestellte kastenförmige Vier-Wege-Multi-Shuttle-Lösung die aktuellen Geschäftsanforderungen besser erfüllen, sich an die Entwicklung des Unternehmens und nachfolgende Geschäftserweiterungen anpassen und dabei helfen, die Pünktlichkeit der Auftragsantwort sicherzustellen und die Effizienz des Unternehmens zu verbessern Unternehmen, und sparen effektiv den Bedarf an Arbeitskräften und Betriebskosten und erzielen signifikante Ergebnisse.
Projektübersicht und Hauptprozess
Dieses Projekt erstreckt sich über eine Fläche von etwa 2.000 Quadratmetern und beinhaltet den Bau eines automatischen dichten Lagerhauses mit einer Höhe von fast 10 Metern.Es gibt fast 20.000 Laderäume.Die Wendebox lässt sich in zwei, drei und vier Fächer unterteilen und bietet Platz für knapp 70.000 Artikel.Dieses Projekt ist mit 15 kastenförmigen Vier-Wege-Multi-Shuttles, 3 Aufzügen, 1 Satz Regalendförderstrecke und vorderem Fördermodul sowie 3 Sätzen Ware-zur-Person-Kommissionierstationen ausgestattet.
Das System wird mit WMS-Software konfiguriert, um eine Verbindung zum ERP-System des Unternehmens herzustellen, und mit WCS-Software konfiguriert, die für die Zerlegung, Verteilung und Ausrüstungsplanungsverwaltung von Arbeitsaufgaben verantwortlich ist.
WMS-Software WCS-Software
Der Produkteingangs- und -ausgangsprozess läuft wie folgt ab:
1. Eingehend
◇Das WMS-System verwaltet die Bindung des Barcodes von Umschlagkarton und Material und legt damit den Grundstein für die Bestandsverwaltung.
◇Vervollständigen Sie die Online-Umsatzbox manuell.Die Umschlagbox gelangt nach dem Scannen des Codes und der Überhöhungserkennung ohne Auffälligkeiten in das Fördersystem.
◇Wendebox, die gemäß der Systemverteilungslogik in das Fördersystem gelangt, wird per Aufzug und Vier-Wege-Multi-Shuttle an die vorgesehene Position transportiert.
◇WMS aktualisiert die Bestandsinformationen nach Erhalt der Anweisung, die Lieferung des Vier-Wege-Multi-Shuttles abzuschließen, und die Lagerarbeiten sind abgeschlossen.
2. Lagerung
Die zu lagernden Materialien werden auf der Grundlage der vorherigen Big-Data-Beurteilung in die drei ABC-Kategorien eingeteilt, und auch die Systemladungsstandortplanung ist entsprechend auf ABC ausgelegt.Der Frachtraum jeder Etage, der direkt auf die Unterspur des Aufzugs gerichtet ist, wird als Materiallagerbereich vom Typ A definiert, der umgebende Bereich ist Materiallagerbereich vom Typ B und die anderen Bereiche sind Materiallagerbereich vom Typ C.
Im Materiallagerbereich des Typs A muss der Shuttle-Wagen beim Aufnehmen und Platzieren dieser Art von Wendeboxen nicht in den Hauptspurmodus wechseln, da er direkt dem Aufzug zugewandt ist, was die Zeit für Beschleunigung, Verzögerung und Wechsel zwischen Unter- und Position spart Hauptspur, daher ist die Effizienz höher.
3. Kommissionierung
◇Das System generiert nach Eingang der ERP-Bestellung automatisch Kommissionierungswellen, berechnet die erforderlichen Materialien und generiert eine Ausgangsaufgabe für Materialumschlagboxen entsprechend der Lagereinheit, in der sich die Materialien befinden.
◇Umschlagkarton wird nach Durchlaufen des Vier-Wege-Multi-Shuttles, des Aufzugs und der Förderstrecke zur Kommissionierstation transportiert;
◇Eine Kommissionierstation verfügt über mehrere Umschlagboxen, die nacheinander bedient werden müssen, sodass die Bediener nicht auf die Umschlagbox warten müssen.
◇Der clientseitige Anzeigebildschirm der WMS-Software ist mit der Anzeige von Frachtrauminformationen, Materialinformationen usw. ausgestattet. Gleichzeitig leuchtet das Licht auf der Oberseite der Kommissionierstation in den zu kommissionierenden Warenraum, um den Bediener daran zu erinnern Verbesserung der Kommissioniereffizienz;
◇Ausgestattet mit mehreren Bestellboxen mit Tastenbeleuchtung an den entsprechenden Positionen, um den Bediener daran zu erinnern, Materialien in die beleuchteten Bestellboxen zu legen, um eine narrensichere Bedienung zu gewährleisten und Fehler zu reduzieren.
4. Ausgehend
Nachdem ein Auftragskarton kommissioniert wurde, übergibt das System ihn automatisch an die Lagerförderstrecke.Nach dem Scannen des Barcodes der Umschlagbox mit dem PDA druckt das System automatisch die Packliste und die Bestellinformationen aus, um eine Grundlage für die anschließende Sammlung, Konsolidierung und Überprüfung zu schaffen.Nachdem die Materialien für kleine Bestellungen mit anderen Materialien für große Bestellungen zusammengeführt wurden, werden sie rechtzeitig an den Kunden versandt.
Für 3PL-Unternehmen, die Autoteile verkaufen, gibt es häufige Probleme bei der Lagerung, Lagerung, Nachfüllung sowie Kommissionierung und Entnahme von Teilen.Während die Betriebseffizienz sinkt und die Unternehmenskosten steigen, bringt es auch größere Schwierigkeiten für die Speicherverwaltung der Hersteller mit sich:
①SKU nimmt ständig zu, es ist schwierig, Waren zu planen und zu verwalten
Herkömmliche Autoteilelager sind meist unterteilt in Palettenlager, in denen hauptsächlich große Teile gelagert werden, und leichte Regale oder mehrstufige Zwischengeschosse, in denen hauptsächlich kleine Teile gelagert werden.Da bei der Lagerung kleiner Artikel die Anzahl der SKUs von Tag zu Tag zunimmt, können die Long-Tail-SKUs nicht aus den Regalen entfernt werden, und der Arbeitsaufwand für die Planung und Optimierung der Verwaltung von Frachtstandorten ist relativ groß.
②Geringe Auslastung der Lagerkapazität
Für das Standardlager steht eine lichte Fläche von mehr als 9 Metern zur Verfügung.Mit Ausnahme des mehrstufigen Mezzanine-Regals mit drei Ebenen besteht bei anderen Regalen für leichte Beanspruchung das Problem, dass der obere Raum nicht vollständig genutzt werden kann und die Miete pro Flächeneinheit verschwendet wird.
③Große Lagerfläche und viele Handhabungskräfte
Die Lagerfläche ist zu groß und die Laufstrecke während des Betriebs ist zu lang, was zu einer geringen Effizienz des Ein-Personen-Betriebs führt, sodass mehr Arbeitskräfte für Auffüllung, Kommissionierung, Inventur und Umschichtung erforderlich sind.
④Großer Arbeitsaufwand beim Kommissionieren und Entladen, fehleranfällig
Lagerhäuser mit manuellem Betrieb verwenden meist die Pick-and-Seed-Methode, da es an narrensicheren Methoden mangelt, und stoßen häufig auf Probleme wie fehlende Codes, das Werfen der falschen Kartons, mehr oder weniger Buchungen, was bei der späteren Überprüfung und Verpackung mehr Personal erfordert.
⑤Steigender Informationsbedarf
Mit dem Aufkommen des Internets der Dinge nimmt die Nachfrage nach Produktrückverfolgbarkeit in allen Lebensbereichen allmählich zu, und Autoteile bilden da keine Ausnahme.Für die Verwaltung von Bestandsinformationen sind intelligentere Informationsmethoden erforderlich.
INFORM ist seit vielen Jahren intensiv in der Autoteileindustrie tätig und verfügt über umfangreiche Erfahrung in den Bereichen Regale und automatisierte Handhabungsgeräte.Allein in der Fertigungsindustrie gibt es fast 100 Fälle von Systemintegration.Die Projektumsetzung umfasst sowohl Hardware als auch Software und kann schlüsselfertige Projekte bereitstellen und das Management sparen.Andererseits verfügt INFORM als börsennotiertes Unternehmen über einen stabilen Geschäftsbetrieb.Es verfügt über ausreichenden Schutz für alle Arten der Risikokontrolle während der Projektumsetzung und der anschließenden Wartungsdienste.Daher entschied sich das Unternehmen für die Zusammenarbeit mit INFORM, um dieses Projekt zu realisieren.
Projektschwierigkeiten und Kernhighlights
Im Designprozess dieses Projekts wurden viele technische Schwierigkeiten überwunden:
◇Es gibt viele SKUs vor Ort, daher hat INFORM ein Wendebox-Trennsystem entwickelt.Die Wendebox kann in 2/3/4 Raster unterteilt werden und mehrere Materialien können in derselben Wendebox platziert werden.Bei der Informationsverarbeitung wird eine genaue Positionierung jedes Gitters in der Wendebox durchgeführt, um sicherzustellen, dass sich die Richtung der Wendebox während der Kommissionierung nicht ändert, was zu Abweichungen im Kommissionierleitsystem führen würde.
◇Aufgrund der Materialmischung verlängert sich die Zeit, die der Bediener für die Bestimmung der Waren benötigt, und die Fehlerquote bei der Beurteilung steigt.INFORM nutzte das Light-Picking-System am Ware-zur-Person-Kommissionierplatz, um die Bediener rechtzeitig daran zu erinnern, die Arbeitseffizienz zu verbessern und Fehler zu reduzieren.
◇Mit der Steigerung des Geschäftsvolumens kann die Effizienz des Lagerein- und -ausgangs flexibel verbessert werden und der Übergang wird reibungslos verlaufen.INFORM hat zur Lösung des Problems eine Vier-Wege-Multi-Shuttle-Lösung eingeführt.Zunächst ist jede Schicht mit einem Shuttlewagen ausgestattet.Später kann die Anzahl der Shuttle-Wagen jederzeit erhöht werden, um mehrere Vorgänge auf derselben Ebene durchzuführen und so die Effizienz zu verbessern.
Durch kontinuierliche Bemühungen zur Überwindung von Schwierigkeiten wurde das Projekt erfolgreich umgesetzt und zeigte während des Implementierungsprozesses viele Lichtblicke:
1. Design des großen und kleinen Schleifenförderleitungssystems
Im Schema stehen drei Kommissionierplätzen jeweils drei Aufzüge gegenüber.Daher wird im normalen Kommissionierbetrieb die von jeder Kommissionierstation benötigte Wendebox direkt in den entsprechenden Aufzug hinein- und herausgefahren.Der Weg ist kurz und die Effizienz hoch. Dies ist der kleine Schleifenweg der Förderstrecke.In anderen Bereichen wie der Lagerung voller Kartons, bei der Kommissionierung, Inventur und anderen Prozessen muss der Umschlagkarton eine horizontale Förderschleife durchlaufen, die durch drei kleine Schleifen verläuft.Dies ist die große Schleife, die Aorta, die jeden Knoten verbindet.
2. Multifunktionales Kommissionierstationsdesign
Der Kommissionierplatz ist mit mehreren Zwischenlagerplätzen für Materialumschlagboxen und Auftragsumschlagboxen ausgestattet.Nachdem die Kommissionierung einer Wendebox abgeschlossen ist, kann der Bediener beim Ersetzen der Wendebox eine andere Wendebox auswählen, was keine Wartezeiten verursacht und die Effizienz gewährleistet.
Die Kommissionierstation ist mit einem Mensch-Computer-Interaktionsbildschirm, einem Lichtkommissioniersystem und einem Knopflicht-Bestätigungssystem ausgestattet, was die Effizienz verbessert und gleichzeitig Fehler verhindert.
Zusätzlich zur Kommissionierfunktion verfügt der Kommissionierplatz auch über eine Inventurfunktion, um sicherzustellen, dass Bediener bei der Durchführung von Wellenaufträgen auch einzelne Materialien inventarisieren können.
3. Unterstützt durch ein ausgereiftes Softwaresystem
Die Autoteile in diesem Projekt erfordern ein schlankes Management und die Ausrüstung muss intelligent geplant werden.Daher werden in diesem Projekt das WMS-System und das WCS-System auf der Grundlage von Standardprozessen entwickelt, um den tatsächlichen Anforderungen gerecht zu werden.
WMS bietet hauptsächlich Funktionen wie herkömmliche Bestandsverwaltung, Bestandsabfrage, Produktrückverfolgbarkeit und Bestandswarnung.Gleichzeitig kann es Bestellinformationen direkt und rechtzeitig aus dem ERP-System importieren, nach dem Zusammenführen von Wellen automatisch mit der Auftragserteilung beginnen, den Ausführungsprozess von Aufträgen verfolgen, Ausführungsergebnisse zurückmelden, Bestandsinformationen aktualisieren und Betriebsdaten sammeln.
Das System ist mit einem WCS-System ausgestattet, das die Arbeitsaufgaben vom WMS-System zerlegt, die Ausführung verschiedener Hardwaregeräte plant und verwaltet.Die Kernlogik umfasst: die Versandlogik mehrerer Vier-Wege-Multi-Shuttles auf derselben Ebene, die Ein- und Ausfahraufzüge, den Schichtwechsel der Shuttle-Wagen, die Planung der Cross-Picking-Stationen für Umschlagboxen usw.
4. Konfigurieren Sie ein Echtzeitüberwachungssystem, um Kunden dabei zu helfen, Betriebsinformationen und wichtige Warnungen rechtzeitig zu verstehen
Vor Ort ist ein großer berührungsempfindlicher Überwachungsbildschirm so konfiguriert, dass er die Betriebseffizienz jeder Ausrüstung und die zugehörigen Parameter der Auftragsausführung in Echtzeit anzeigt, sodass Manager, Führungskräfte und Besucher vor Ort den Betrieb vor Ort verstehen können Status auf einen Blick.
Gleichzeitig kann der große Überwachungsbildschirm wichtige Alarminformationen in Echtzeit anzeigen und das Betriebs- und Wartungspersonal durch Ton und Licht daran erinnern, Alarme rechtzeitig zu bearbeiten, um die Betriebseffizienz sicherzustellen.
Warum uns wählen
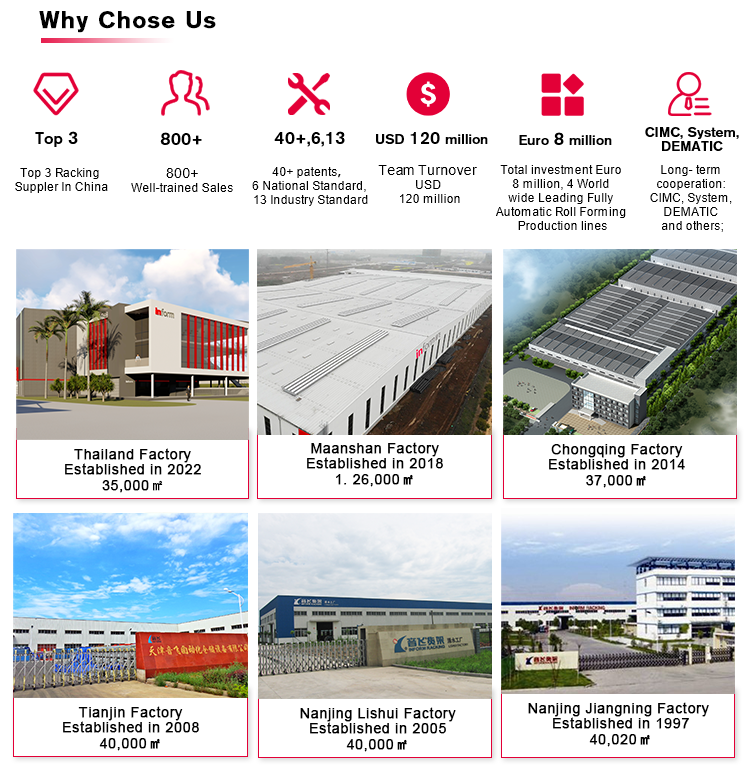
Die Besten 3Regallieferant in China
DerEinzigerA-Aktien-gelisteter Regalhersteller
1. Die NanJing Inform Storage Equipment Group ist ein börsennotiertes, staatlich kontrolliertes Unternehmen, das sich auf den Bereich der logistischen Lagerlösungen spezialisiert hatseit 1997(26langjährige Erfahrung).
2. Kernbusiness: Racking
Strategisches Geschäft: Automatische Systemintegration
Wachsender Business: Lagerbetriebsdienst
3. Informieren Sie die Eigentümer6Fabriken, mit über1000Mitarbeiter.Informierenbörsennotierte A-Aktie am 11. Juni 2015, Börsenkürzel:603066, wird zumerstes börsennotiertes Unternehmen in China's Lagerwirtschaft.
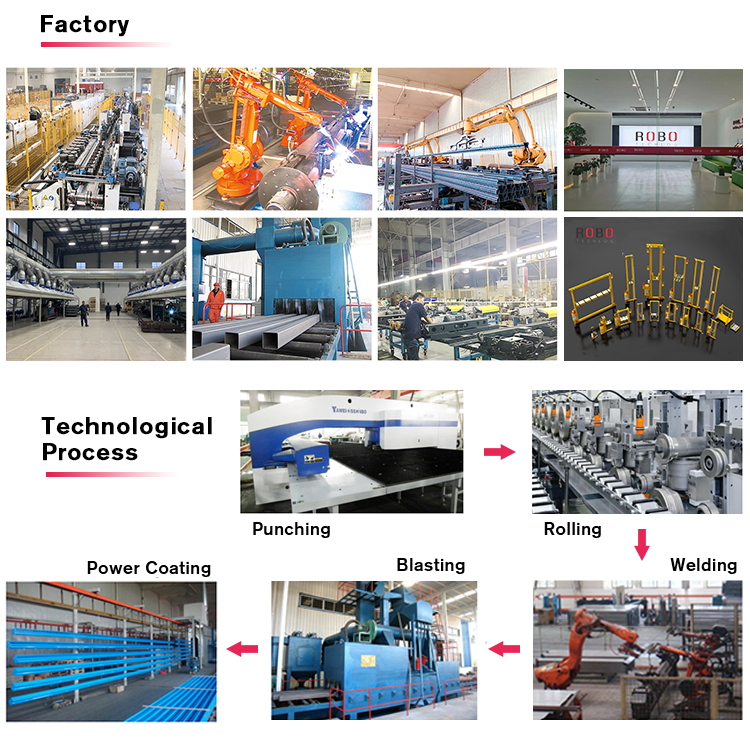
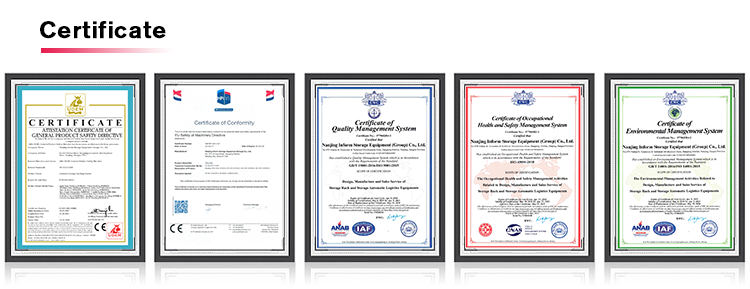
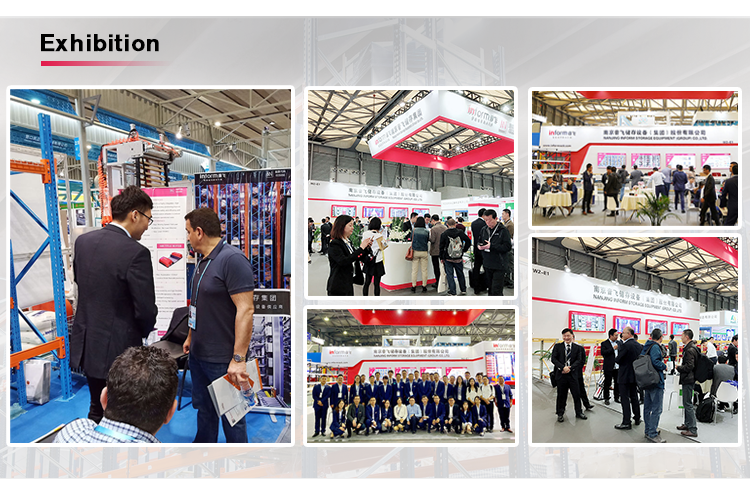
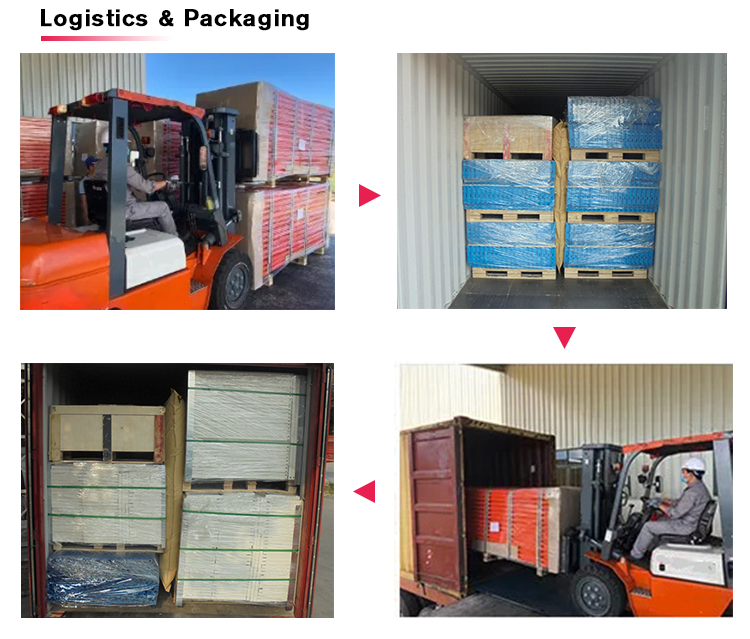
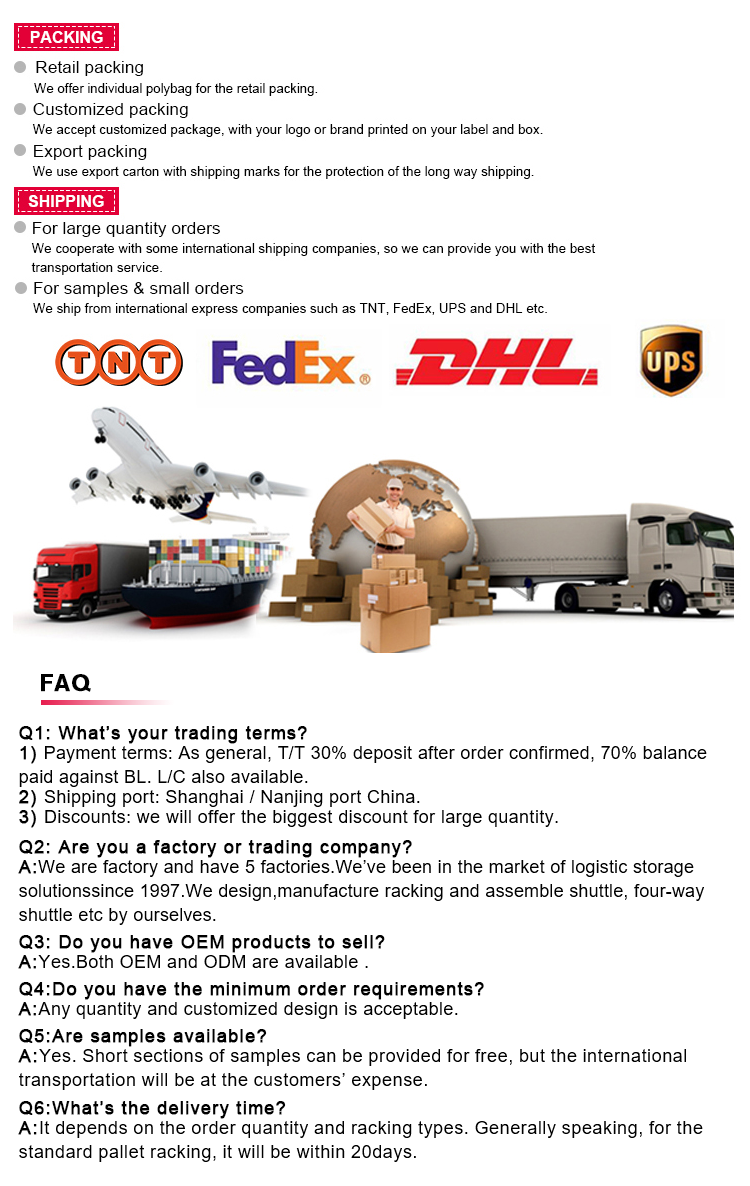